Jeder Tropfen zählt
Rund um den Globus arbeitet Freudenberg Performance Materials daran, in der Produktion immer weniger Wasser zu verbrauchen und mehr Abwasser denn je zu recyceln. Der Einsatz lohnt sich, wie drei Beispiele aus Taiwan, Indien und Südafrika zeigen.
Mingta Yang kann sich gut daran erinnern, als Wasser für ihn und seine über einhundert Mitarbeiter am Standort von Freudenberg Performance Materials in Yangmei, Taiwan, schlagartig zu einem Thema wurde. Mitte 2015 wuchs die Produktion, die Yang verantwortet, deutlich. Ein Teil der Vliesstoff-Herstellung aus China war in den Inselstaat verlagert worden. Die Herausforderungen, die sich dadurch für das Unternehmen in der Stadt Yangmei ergaben, waren groß: Die Abwassermenge wuchs, es mussten mehr Chemikalien eingesetzt werden und die Qualität des rückgewonnenen Wassers verschlechterte sich.
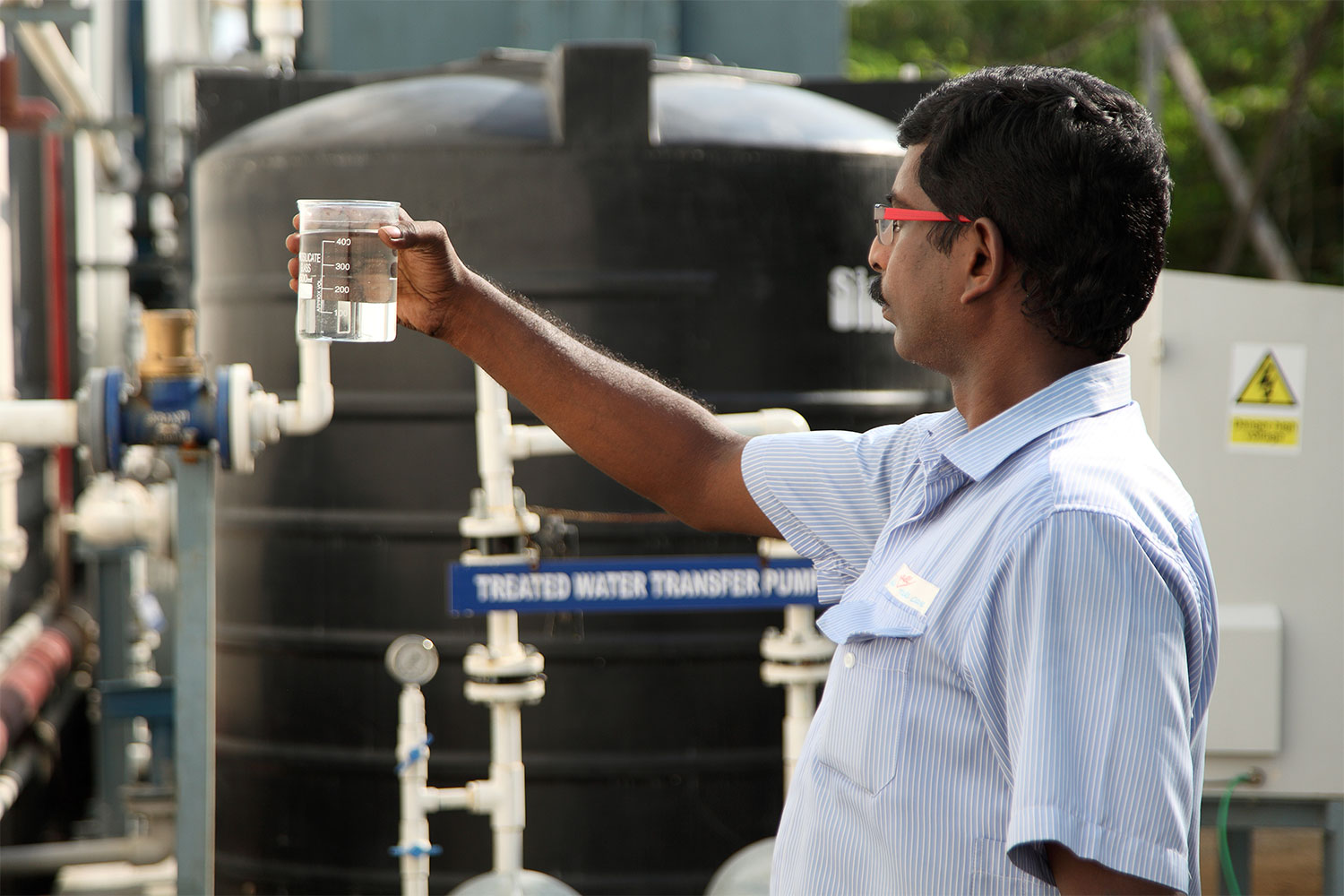
Produktionsleiter Krishnamoorty Guptha Dasaradhan prüft die Qualität des gereinigten Wassers in Chennai.
Ungefähr zur gleichen Zeit machte sich auch Gunasekaran Sivasailam Gedanken über das Thema H2O: Der Leiter des Werks im indischen Chennai, in dem ebenfalls Vliesstoffe hergestellt werden, befasste sich mit der ausreichenden Versorgung seiner Produktion, denn in der Metropole mit ihren rund 12 Millionen Einwohnern wurde und wird grundsätzlich mehr Grundwasser verbraucht als durch Regen wieder aufgefüllt wurde. Die Folgen: Böden versalzen und teilweise dringt Meerwasser in die Grundwasserspeicher ein. Die Versorgung von Bevölkerung und Industrie ist nicht sicher.
Yang, Sivasailam und ihre Teams reagierten: Sie analysierten den Wasserkreislauf und -einsatz in ihren Betrieben, griffen auf das Wissen externer Forscher und Experten sowie anderer Standorte zurück und erarbeiteten so die für ihre Werke optimalen Lösungen, um mit weniger Wasser auszukommen und so viel wie möglich davon wieder aufzubereiten. Damit stehen sie nicht alleine. „An all unseren Standorten arbeiten wir kontinuierlich daran, sparsamer und nachhaltiger mit Wasser umzugehen“, sagt Detlef Kürvers, der bei Freudenberg Performance Materials die globale Funktion Gesundheitsschutz, Umweltschutz und Arbeitssicherheit leitet und regelmäßig rund 23 Produktionsstandorte auf der ganzen Welt besucht und berät. „Die Fortschritte sind beachtlich, denn die Teams teilen ihr Wissen über funktionierende Technologien und Prozesse im globalen Freudenberg-Netzwerk. So profitieren alle voneinander.“
Weniger ist Mehr
In Yangmei wurde ein vollständig neuer Technologie-Mix installiert, um den Wassereinsatz – pro Jahr werden in der Produktion rund 21 Millionen Liter benötigt – effizienter zu machen. „Unser Abwasser wird in elf Schritten gereinigt“, sagt Standortleiter Yang. Dabei werden Wasser und Schlamm mit Hilfe von Ultrafiltrations-Membranen in mehreren Durchläufen voneinander getrennt. Anschließend werden durch die so genannte Umkehrosmose weitere Schmutzteilchen aus dem Abwasser gefiltert. „Der Anteil des in der Anlage verwendeten recycelten Wassers stieg so seit 2016 kontinuierlich von 4,3 auf 60 Prozent. Außerdem verbrauchen wir jährlich 200 Tonnen weniger Chemikalien“, erläutert Yang. Das neue Verfahren führte überdies zu einer Verbesserung der Qualität des Oberflächenwassers und es senkte die Betriebskosten um 23.000 Euro pro Jahr. Mit diesem innovativen Ansatz gewann das Team aus Taiwan sogar beim internen Freudenberg-Award „We all take care“ im Jahr 2017.
Zu 100 Prozent recyceltes Abwasser
Am Standort in Chennai ging man aufgrund der besonders kritischen Wasserlage noch einen Schritt weiter. Inzwischen wird dort das gesamte Abwasser aus der Herstellung gereinigt und wiederverwendet. Dazu entwickelte das Team für Gesundheitsschutz, Umweltschutz und Arbeitssicherheit von Freudenberg gemeinsam mit dem „Centre for Scientific Industrial Research Institute“ und der „Industrial Waste Management Association“ in Chennai einen geeigneten und effektiven Filtrationsprozess. Nach monatelangen Analyse- und Labortests wurde Mitte 2016 eine mehrstufige Filter-Technologie in Betrieb genommen, die aus verschiedenen Komponenten besteht und perfekt zu den Anforderungen in Chennai passt.
„Damit gelingt es uns, das Abwasser zu 100 Prozent zu recyceln“, sagt Sivasailam. „Außerdem ist die Qualität des gefilterten Wassers deutlich besser und unser Verbrauch reduzierte sich insgesamt deutlich: Für ein Kilogramm der bei uns produzierten Textilien benötigen wir heute nicht mehr 4,4 Liter Wasser, sondern nur noch 2,7 Liter.“ Ein zusätzlicher Pluspunkt: Die während des Filterprozesses entstehenden Feststoffe werden gesammelt und an die Zementindustrie verkauft, der sie als Brennstoff dienen.
Kleine Veränderungen, große Wirkung
Angesichts des Zustands der globalen Wasserressourcen sind die Verbesserungen an den FPM-Standorten wichtiger denn je. Das „World Ressource Institute“ berichtete im Herbst 2019 in einer Untersuchung, dass sich seit den 1960er-Jahren die entnommene Grundwassermenge weltweit mehr als verdoppelt habe. 44 Staaten – darunter Indien und Südafrika – leiden unter hohem bzw. sehr hohem Wasserstress: Die Wasserversorgung ist prekär. Bei zu wenig Niederschlag oder längeren Hitzeperioden droht akuter Mangel und eine dauerhafte Unterversorgung.
Dass ein solches Szenario schnell real werden kann, bekam das FPM-Werk in Kapstadt im April 2018 zu spüren. Damals stand die südafrikanische Metropole kurz davor, Einwohnern und Unternehmen das Wasser abzudrehen. Inzwischen hat sich die Lage zwar wieder entspannt, aber neue ausgedehnte Trockenperioden sind nicht unwahrscheinlich. „Wir haben deshalb Schritt für Schritt Maßnahmen ergriffen, damit unsere 70 Mitarbeiter achtsamer und sparsamer mit Wasser umgehen“, sagt HSE-Manager Christian Tiede. „Für sich genommen klingen die Veränderungen bisweilen simpel, in Summe aber lässt sich damit richtig viel erreichen.“
Diese praktischen Tipps haben eine Menge bewirkt, weil sich alle Mitarbeiter nach ihnen richten.
Christian Tiede, HSE-Manager
Die Klimaanlagen zum Beispiel werden heute nur noch an sehr heißen Tagen eingeschaltet und nicht – wie früher – ständig. „So lange wir eine gute Ventilation gewährleisten können, bleiben unsere Klimaanlagen aus, und das ist meistens der Fall“, so Tiede. Außerdem wurden zwei offene Wassersysteme geschlossen, sprich in einen Wasserkreislauf verwandelt, und alle undichten Stellen in der Produktion ausfindig gemacht und repariert. Ergänzend setzte man auch beim Verhalten an: Den Mitarbeitern wurden in Trainings und Workshops die Möglichkeiten verdeutlicht, im Arbeitsalltag Wasser zu sparen, etwa indem Wasserhähne sorgfältig geschlossen werden oder Maschinen nicht minutenlang mit fließendem Wasser aus einem Schlauch gereinigt werden, sondern schlicht mit einem Eimer Wasser und einem Lappen.
„Diese praktischen Tipps haben eine Menge bewirkt, weil sich alle Mitarbeiter nach ihnen richten“, sagt Tiede und die Zahlen unterstreichen das: Im Jahr 2019 liegt der monatliche Wasserverbrauch bei rund 426 Litern, 68 Prozent weniger als 2016. Das Ende der Fahnenstange ist aber noch nicht erreicht: In Kapstadt entsteht bald eine Anlage zur Sammlung und Filtrierung von Regenwasser, das dann unter anderem zur Reinigung und in den Toiletten verwendet werden soll. Und einige tausend Kilometer entfernt, im indischen Chennai, hegt man ähnliche Pläne – der Kommunikation und dem Austausch im Freudenberg Performance Materials-Netzwerk sei Dank.