Freudenberg sheds light on the friction gap
Environmentally friendly and informative: Freudenberg and Fraunhofer develop virtual material probe and win the Stifterverband science prize for joint research.
Tires, brakes, seals: Wherever surfaces come together, there will be friction – and with it, wear. Only a few atoms decide whether power plants run smoothly and vehicles run efficiently. Understanding tribology, the science of friction, wear and lubrication, and designing products to be more efficient and longer lasting requires a look at the friction gap on the atomic level – impossible to see with the naked eye.
So how do you make tribological processes visible? Where many are still stumbling around in the dark, seal manufacturer EagleBurgmann, a Freudenberg Business Group, is shedding light on the friction gap with its virtual material probe, together with the Fraunhofer Institute for the Mechanics of Materials IWM. At this year’s Fraunhofer Annual Conference in May, the research team received the Stifterverband “Joint research” science prize for their long-standing collaboration and innovative results.
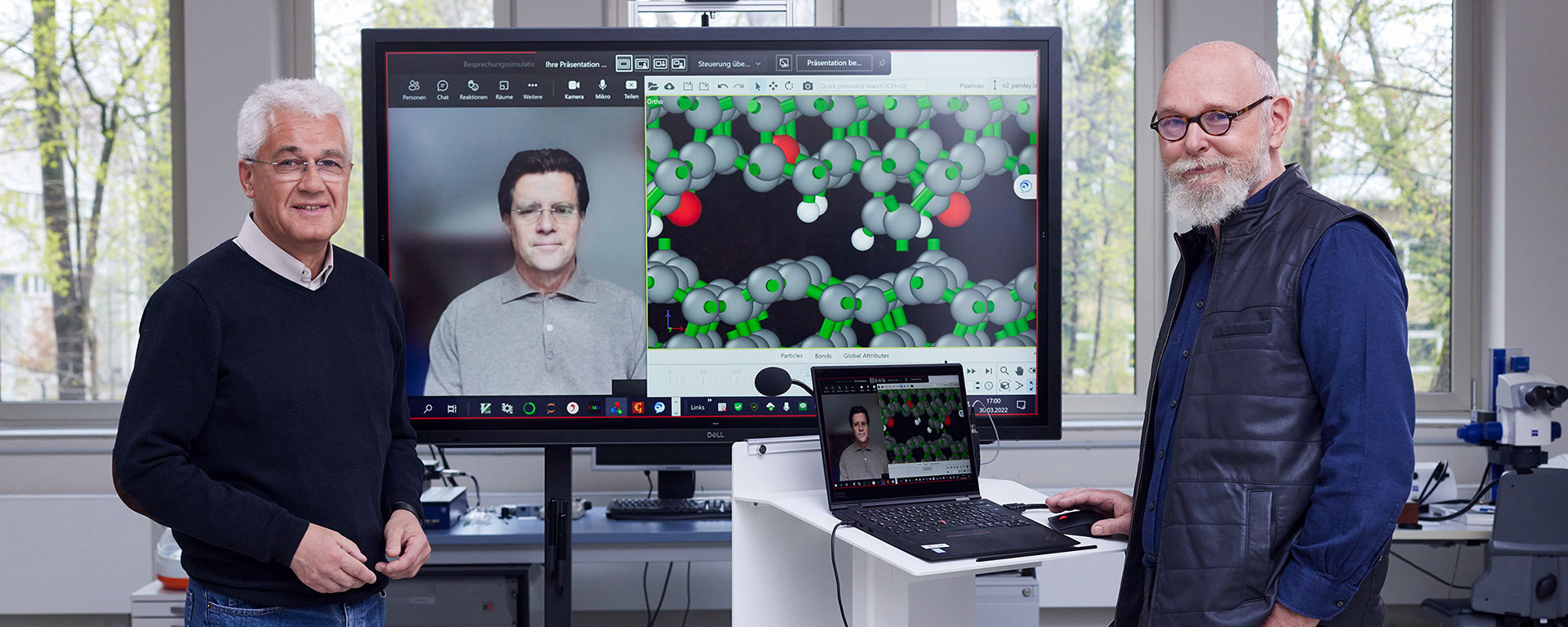
The winners of this year’s Stifterverband science prize for joint research. From left to right:
Prof. Dr. Matthias Scherge, Dr. Joachim Otschik and Prof. Dr. Michael Moseler.
Mechanical seals are installed in applications such as pumps and compressors used in power plants, the food industry or mining, where they are exposed to extreme thermal, mechanical and chemical conditions. Reliability and longevity are essential properties of these seals since the costs of failure or downtime run into the millions, making them a major risk. Diamond coatings on the components in mechanical seals that rub against each other help protect them from wear and ensure a long service life. Fluctuations in the friction coefficient can still occur, however, because even the hardest diamond surfaces wear off over time. Until now, it was not clear what causes these fluctuations and how EagleBurgmann can keep the friction to a minimum at all times. The team of researchers, made up of Dr. Joachim Otschik, Senior Director Research & Development at EagleBurgmann, as well as Prof. Dr. Michael Moseler, Prof. Dr. Matthias Scherge of the Fraunhofer Institute for Mechanics of Materials IWM, developed the key to success: a virtual material probe that combines simulations on multiple scales with the results of real experiments. It provides a virtual view of the microscopic movement and interactions between atoms, making tribological processes visible and controllable on the atomic level. For the first time, this simulation enables Freudenberg to understand tribological processes more precisely than ever before and design products to be even more efficient and durable.
The virtual material probe is useful in any application in which two objects rub against each other and are lubricated by an atom-thin film of liquid. This is the case in the drive train of electric vehicles or in the compressors of heat pumps, to name two examples. “Experiments alone are not enough for us to understand the effects of friction nor the influence of the extremely thin film – the field of tribological contact is practically in the dark,” explains Scherge. His colleague Moseler adds: “But the virtual material probe lets us zoom in from the millimeter scale to the atomic scale, and in extreme cases, even to the quantum mechanical level of electrons, in order to understand the binding relationships in the friction gap.” The simulation provides answers to the question of which pairings of materials slide particularly efficiently and thus enable high-tech seals with hardly any leakage, friction or wear .
There is a unique synergy between us and Fraunhofer IWM, which is growing and picking up speed. Together, we have created a virtual material probe that is unique worldwide in this form and complexity
Dr. Joachim Otschik, Senior Director Research & Development at EagleBurgmann
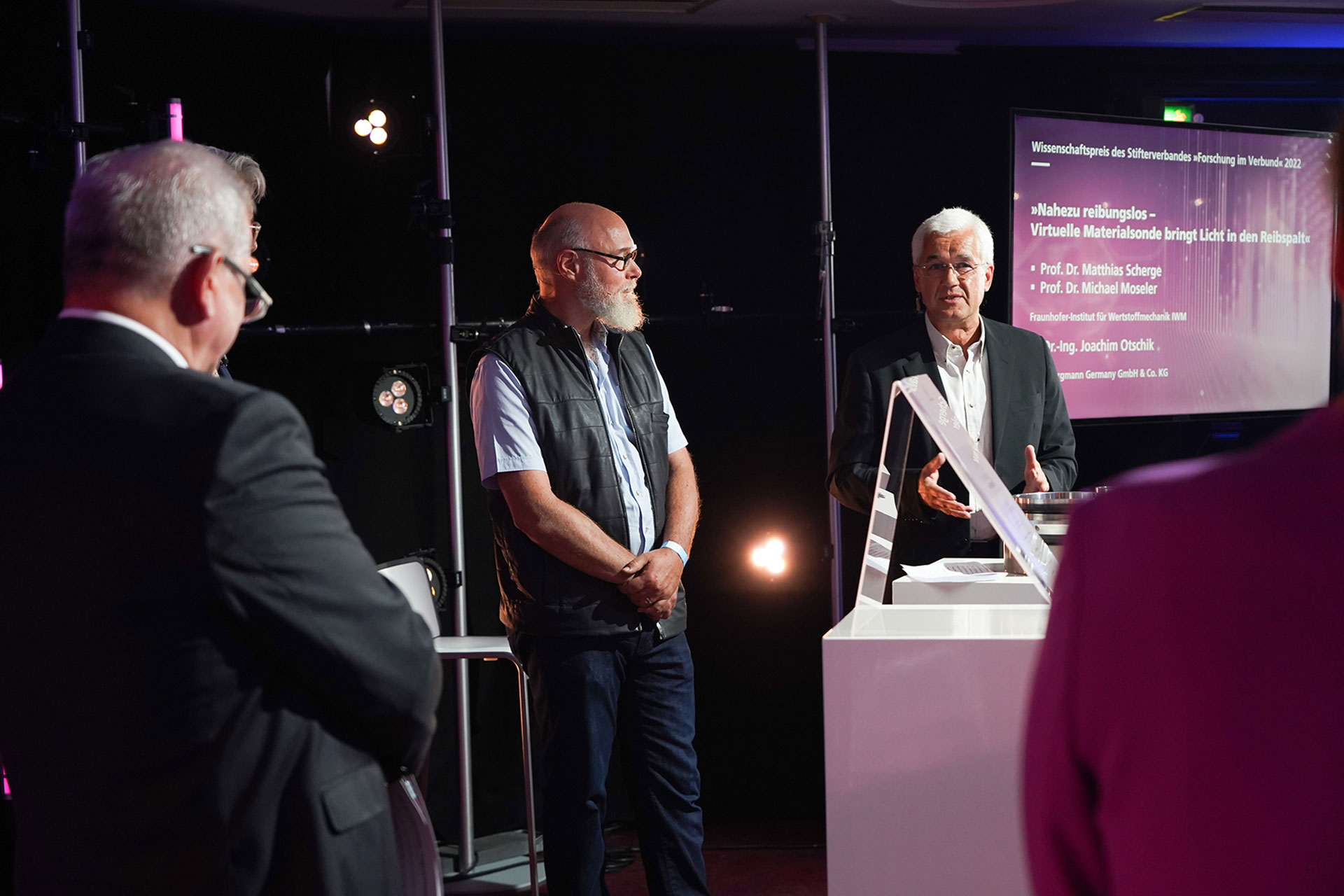
From left to right: Prof. Dr.-Ing. Reimund Neugebauer, President of the Fraunhofer Association, Prof. Dr. Michael Moseler, Head of Multiscale Modelling and Tribosimulation Group at Fraunhofer IWM as well as Prof. Dr. Matthias Scherge, Tribology Business Unit Manager at Fraunhofer IWM at the Fraunhofer annual conference.
The development of the virtual material probe was made possible by almost two decades of collaboration by the research team. “There is a unique synergy between us and Fraunhofer IWM, which is growing and picking up speed. Together, we have created a virtual material probe that is unique worldwide in this form and complexity,” says Otschik. He goes on to say: “The atomistic simulation, which we already earned us the Freudenberg Innovation Award in 2019, is characterized by joint work with the Freudenberg companies EagleBurgmann, Freudenberg Sealing Technologies, Klüber Lubrication and Freudenberg Technology Innovation as well as the Fraunhofer Institute – true to Freudenberg’s motto of ‘Innovating together’.” And EagleBurgmann is not the only one to benefit from the virtual material probe, the entire Freudenberg world does too. “EagleBurgmann is the driving force behind the use of atomistic simulation in other Freudenberg Business Groups as well – thanks to our colleague Dr. Rüdiger Braun, who is in charge of technical coordination at the Freudenberg Chemical Specialties Business Group,” explains Dr. Ravindrakumar Bactavatchalou, Head of Tribology at Freudenberg Technology Innovation. The virtual material probe has opened many doors in the Freudenberg world since then: “For one thing, new jobs can be created, and the atomistic simulation also serves as a tool for the entire Freudenberg product portfolio. It significantly reduces development times, which saves on financial resources as well as materials,” adds Otschik.
The virtual material probe will also solve many problems in the future concerning issues such as sustainability. For instance, it will play an important role in new energy sources, fuels and the emerging hydrogen economy. The virtual material probe can be used to minimize CO2 emissions. After all: Saving energy starts with friction-free processes – the less friction there is, the less energy is lost. Freudenberg has set itself the goal of building up a broader basic understanding of simulation techniques so that it will be equipped to tackle future tribological challenges. The first milestone is the virtual material probe, which will permanently change the world of friction processes.
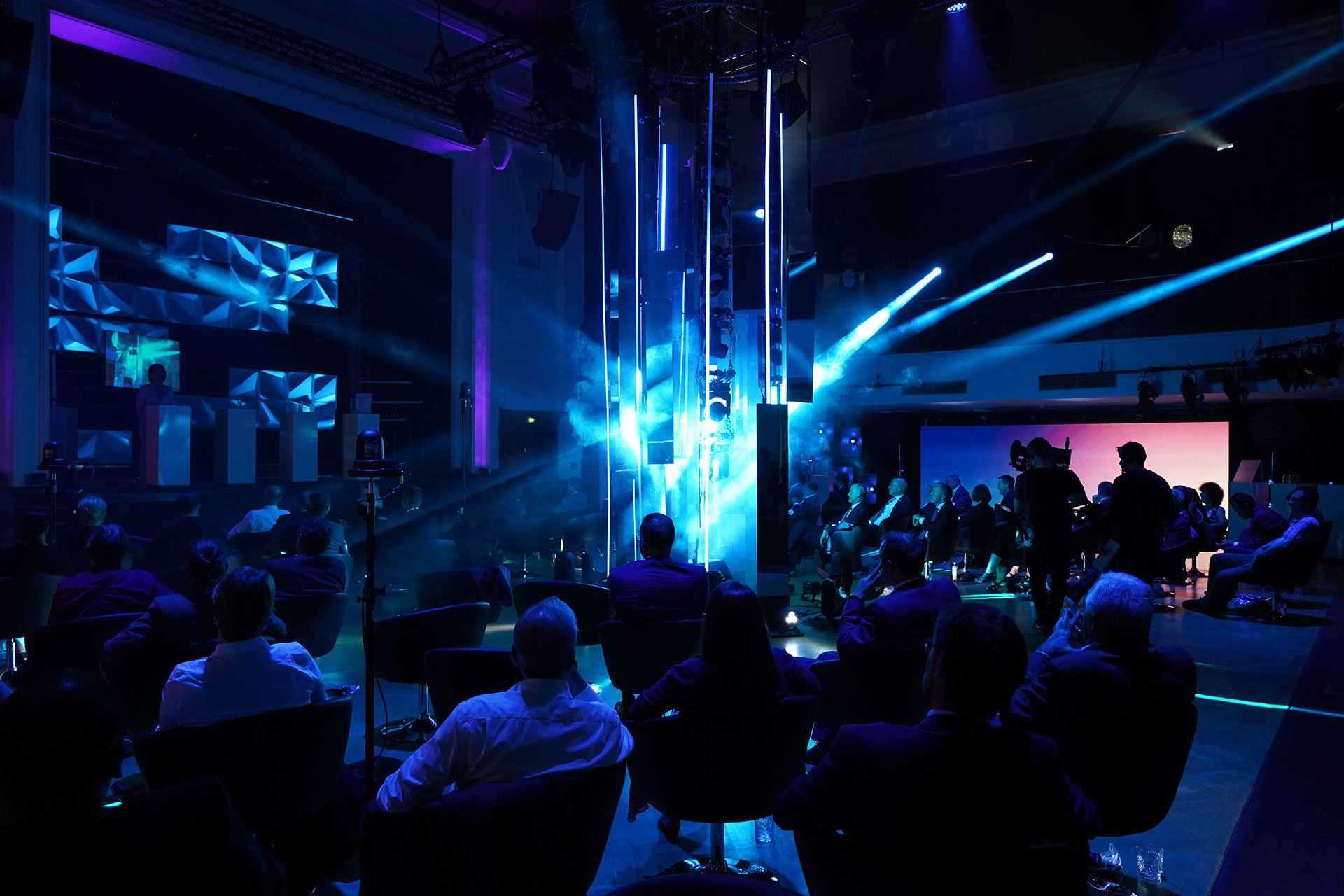
A look at the Fraunhofer annual conference on May 19th, 2022, as a hybrid event in Hamburg.